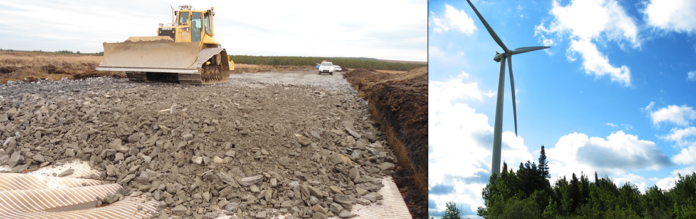
Subsidies and federal energy policies get most of the headlines, but with the increasing size of wind turbines and the scale of wind farms, few sites can be developed without soil reinforcement technologies. Geosynthetics provide the stable base for construction works and long-term access on wind energy sites.
On-shore wind turbine hub heights increasingly crest 100m, and some are approaching 150m. heading towards 150m. Rotor diameters can exceed 125m. While many turbines are still in the 3 MW range, large turbines are seeing 7.5 – 8+ MW. Hub heights are essentially twice as tall as just 10 years ago and the energy output is four times greater.
Off-shore turbines, which are garnering huge interest now, are being designed even larger.
For on-shore applications, supporting the enormous weight of a turbine (more than 200 tons) frequently requires geosynthetics, as much to support construction (e.g., cranes) as to provide long-term soil stability and dependable access.
REINFORCING WIND ENERGY
Wind farms require space, of course, and it is not uncommon for the soils on these more remote sites to require stabilization technologies in order to support high loads. The larger the wind farm array, the more roadways will need to be constructed between the turbines. Miles of road may be needed on a utility-scale site.
Efficiency is stressed in these road networks. A developer wants to minimize the amount of roadway to be constructed. Also, the developer wants to avoid having to use public roads, as much as possible, between turbines.
In an optimally designed site, once crews are working on a turbine they will not need to “leave” the site to assemble the next. They hope to move cranes and other key equipment from one pad to the next without public roadways, as entering them with such large loads may require special permitting or equipment disassembly.
Crane axels must carry loads in excess of 200,000 lb.—not exactly what conventional roads are rated for.
Furthermore, the efficiency and cost control of the on-site roads will depend on minimizing land disturbance and preventing road or operational safety problems, such as rutting. Hence, geosynthetic reinforcement is utilized to stabilize the subgrade sooner, which reduces the amount of soil needed to be excavated and replaced in road construction.
GEOSYNTHETICS IN WIND ENERGY PROJECTS
Geogrids and high-strength geotextiles provide enormous benefit to wind farm road and crane pad construction. They increase subgrade and flexural stiffness. They reduce vertical and shear stresses. They minimize or prevent migration of fines, reduce aggregate need, and minimize excavation.
All of these benefits not only make wind energy sites more economical but in many situations simply possible.
Examples of this utility are numerous and able to be found throughout the world’s wind energy infrastructure.
HUESKER’s geogrids have been used in a number of wind energy applications too. New York’s High Sheldon Wind Farm, for example, produces roughly 130 MW of power to support 60,000+ homes. The turbines have largely been installed on active agricultural lands, providing side income for those operations while taking advantage of the elevated terrain at those locations to harness the area’s strongest winds. This provides greater output and facilitates efficient delivery of power to the town.
The construction site loads in New York were around 5000 psf, making geosynthetics a must. The 17-ft.-wide rolls helped expedite construction by reducing the need to cut from additional rolls to reach the necessary width.
NAUE has excelled in wind farm constructions internationally with composite reinforcement solutions like Combigrid®, which embeds a durable nonwoven geotextile within a high-strength Secugrid® geogrid. This delivers soil separation, filtration, and reinforcement characteristics in a single roll. This solution provides multiple layers of road subgrade stability in a single layer for quick, substantial ground improvement.
The company has also been involved in geosynthetic-based scour protection for major off-shore wind turbine installations.
TenCate’s high-strength reinforcement geosynthetics (e.g., Mirafi® RSi) have been used to enable construction of wind farms internationally, including the Netherlands’ tallest turbine: a 280-ton, 135m tall (hub height), 7.5 MW Enercon E-126. The tip height of the blade brings its size to 198m. Without the use of the geosynthetic reinforcement, it would not have been economically feasible to construct the crane pad that was needed to support the construction works.
GREATER SUSTAINABILITY IN CONSTRUCTION
The sustainability benefits of wind energy rest not just in the renewability of the energy source. Geosynthetic reinforcement, in strengthening soil more efficiently, requires less land disturbance than would be required to build wind farms without reinforcement. Significantly less soil must be carved into to achieve the appropriate access road and construction platform bearing strength when geosynthetic layers are included. Aggregate fill may be reduced by up to 40%, and over the course of acres of infrastructure this represents substantial time, energy, and cost savings in construction.
The carbon footprint of the on-site construction is greatly reduced, as is the transport to the site of heavy aggregate in polluting trucks.
By reinforcing soils efficiently, wind farms are built faster, more economically, and more sustainably.
RESOURCES
HUESKER: www.huesker.com
NAUE: www.naue.com
Tencate: www.tencate.com
Associations
American Wind Energy Association: www.awea.org
Canada Wind Energy Association: www.canwea.ca
European Wind Energy Association: www.ewea.org
Global Wind Energy Council: www.gwec.net
good application , however economic advantage purely depends upon the cost of locally available material