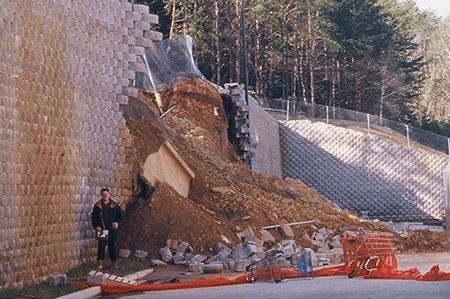
In 2004, Geosynthetica’s Director Elizabeth Peggs, Lara Costa, and founder Dr. Ian D. Peggs, P.E. (I-CORP International) created a white paper that proposed a Geosynthetics Risk Management and Loss Control Program (GRMP). Targeting insurers of construction projects, the program aimed to establish the need for expert design review to prevent costly failures that might result from improper use, poor selection, or misunderstanding of geosynthetics.
Four case studies were presented (PDF of white paper). They emphasized how the use of geosynthetics and design review could provide substantial security and savings to potential insurance / litigation claims by reducing the risk of failure.
- A shopping center retaining wall failure cost $600,000 to repair. More than 25% of the original structure had to be rebuilt. Inappropriate design and specification was the cause, and it could have been prevented with $20,000 of preventive review—at no cost to the insurer.
- A golf course at a hotel development incurred a failure cost of $1.3 million for a 6.5-acre irrigation pond’s failure due to using low-cost, inexperienced labor, which was an inappropriate decision for the liner type and scale of construction. A certified liner installer (who would have cost only $15,000 more initially for the $36,000,000 development) could have prevented the problem. In the end, the experienced installer was hired—to reconstruct the pond properly after all of the failure costs had been realized. The insurer in this instance, again, would not have taken on any cost had it required the use of a certified installer.
- An anaerobic digester produced more than $21 million in failure-associated costs by using a poor design, hiring a less-experience installer, and having improperly specified liner material on site. The upfront savings for these decisions was approximately $40,000. The end cost, however, was more than 500 times greater. It would have cost the insurer nothing to require proper practices and experience.
- The repeated failure of HDPE-lined, concrete, solvent containment tanks for a copper and uranium mine operation was blamed on poor installation practices due to continual, rapidly developing weld failures in the liner. However, the true cause was improperly specified material. The specific geomembrane selected could not contain the type of solvent on site. It was not the right liner to use. At the time of the white paper authoring, the project had shown a failure and litigation cost of close to $23 million. Again, the insurer would not have realized any cost to require expert review of this sensitive installation design and material specification.
For the four projects combined, the factor of cost of material purchased versus repair was 17.9.
For multi-million dollar installations, a USD $10,000 – $40,000 design investment in design review, CQA, or experienced installation work is fairly small. Yet, the commonality in the case studies showed that basic design review and experienced installation was not valued, even though those steps could have prevented expensive failures. These projects represented MILLIONS of dollars in redesign, reconstruction, and litigation costs.
NEED FOR GEOSYNTHETICS RISK MANAGEMENT TODAY
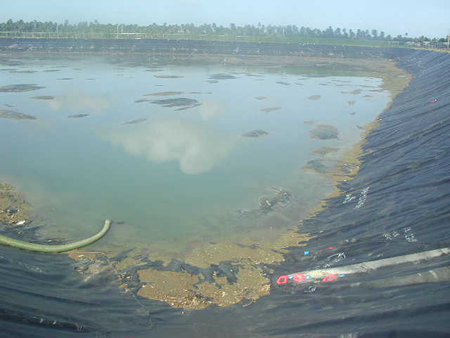
The Geosynthetics Risk Management and Loss Control Program (GRMP) white paper was presented at the Insurance Risk Management Institute (IRMI) conference in November 2004 in Orlando. The presentation was enhanced by studies from the surety field, which showed that 36% of construction companies failed due to poor performance. Also, analysis of insurance industry risk management and loss prevention matrixes revealed nearly 40 areas in direct agreement between the proposed Geosynthetics Risk Management Program and the insurance industry’s best practices for risk management in construction insurance.
However, the response from the insurance field was tepid.
The roles of geosynthetics may have been too little understood by insurers in 2004. Geosynthetics, despite being essential to the economical and performance-related objectives of so many projects, are a small portion of geotechnical works. To the less familiar, a 60-mil liner might not seem very important within a 2 – 3 ft. barrier. For a project such as the failed irrigation pond on the golf course, the liner cost was only 0.3% of the construction. The simple $15,000 expenditure that could have prevented a $1.3 million failure would not have stood out as an oversight in the project to an insurer unfamiliar with geosynthetics.
If we apply the same risk management analysis to current events, we will continue to find expensive failures that could be prevented by experienced review of designs, utilization of experienced installers, and greater consideration of the long-term risks and costs associated with failures.
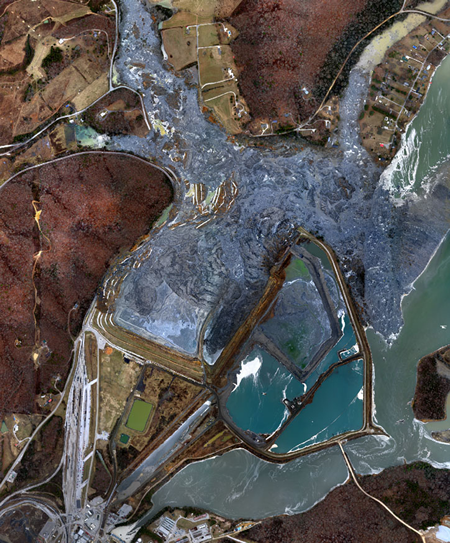
The coal ash industry is the easiest place to see this now. An unlined earthen berm at a facility in Kington, Tennessee failed in 2008 and led to a three-year environmental cleanup that cost more than USD $1 billion. The facility owners had declined proposals to redesign the facility with a liner in the early 2000s. One report suggested full facility redesign for safety at that time would have cost $25 million, a large portion of which would have been associated with adding an engineered geosynthetic lining system.
The facility opted instead to use significantly lower cost drainage improvements. The end result is that more than 40 new facilities could have been built for the price of this one failure.
Those facilities will now be built. All utilities and companies involved in future coal ash storage site construction will be required to use geosynthetics for new construction and closure of the existing 700+ sites. The cause is not just Kingston. Multiple coal ash storage sites have suffered failures in the past 10 years. Federal regulation became inevitable because the risk management analysis in this sector did not place real value on geosynthetics in containment.
Glen Toepfer of CQA Solutions has argued this point perhaps most effectively in the past couple years. He notes that for mine tailings facilities, coal ash storage, waste management, water resource conservation, industrial processing, and so many other containment sites, facility owners should not think of geosynthetics as an upfront cost; rather, geosynthetics should be viewed as long-term assets. They reduce costs, lower risk, and improve sustainability metrics. For sectors such as mining, they actually improve containment and processing of ore; meaning, they produce stronger mine ROI through more substantial ore yields.
THE TAKEAWAY
Building something right the first time is the most important thing we can do. Ensuring that geosynthetics are properly utilized is one step along that path. Ensuring that insurers understand the value of geosynthetics from design, CQA, and installation perspectives is another.
Perhaps it is it time to revive the Geosynthetics Risk Management Program effort.
**
Chris Kelsey is the editor of Geosynthetica. Send project stories, ideas, questions, and site photographs to chris@geosynthetica.net. Your contributions to Geosynthetica’s publishing community are encouraged.