Stephen Wilk, Colin Basye, Dingqing Li, and Brad Kerchoff write on some roles for geosynthetics in railroad applications, such as for ballast pockets and flooded cuts. A version of this article was published as a peer-reviewed paper in the GAP 2019 transportation engineering conference proceedings. Minerva TRI, Geosynthetica’s publisher, organized GAP.
Introduction
Maintaining a properly functioning track substructure is important for railroad operations and asset management because poor substructures can often result in increased track geometry degradation and decreased rail, tie, and fastener lifespans. This can decrease operational capacity due to slow orders and increases track maintenance costs.
The functional railroad track substructure consists of four major components: ballast, subballast, subgrade, and drainage (Li et al., 2016; AREMA, 2018). Ballast is typically made up of one to two-inch angular crushed rocks that provides a strong trackbed, distributes loads to the subballast and subgrade, and allows the drainage of water. The subballast is an intermediate layer that acts as a barrier between the large ballast particles and the subgrade; however, it can serve as a second foundation layer to help distribute loads if a weak subgrade is present. The subgrade is usually the natural soil but can also be fill in the case of embankments. External drainage typically consists of ditches that allow for the runoff water to be directed away from the track.
Over time, the track substructure can experience a wide range of issues from the breakdown of ballast, inadequate drainage, and subgrade deformation, each of which requires different maintenance or remedial solutions to address the root cause of the issue. One long-term strategic research goal of Transportation Technology Center, Inc. (TTCI)’s track substructure program is to better organize and understand which solutions have shown to be successful for each substructure issue and help determine variables that may help contribute or impede the success of the that solution. This article presents two recent case studies performed by TTCI that show how geosynthetics helped mitigate two common substructure issues in railroad applications.
RELATED: Estimation of Soil-Water Characteristic Curves in Fouled Ballast
Railroad Applications: Ballast Pocket in Railroad Embankment
Ballast pockets are a common subgrade issue that often results in higher track geometry degradation rates and therefore requires more track maintenance, leading to lower operational capacity. Remediation techniques that can reduce track geometry degradation at ballast pockets are available if the root cause is identified and addressed (Basye and Wilk, 2019). The underlying mechanism producing ballast pockets is typically a soft-subgrade embankment that progressively deforms vertically and laterally over time (Li et al., 2016; Basye and Wilk, 2019). New ballast is added during track maintenance to restore track geometry elevations. This cycle can develop into a ballast pocket over time. An illustration of a ballast pocket is shown in Figure 1. Ballast pockets can range from a local 2-ft section to over 15-ft deep sections that span hundreds of feet along the track. Ballast pocket deformation also is frequently non-symmetrical under the track, resulting in lateral or vertical deformation that manifests as cross-level and alignment issues.
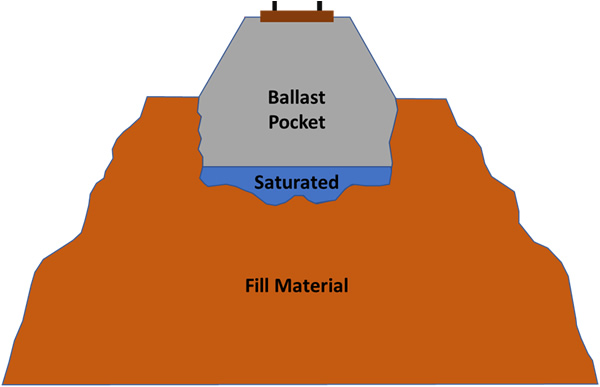
Soft-subgrade embankments typically result from the initial construction, often over 100 years ago, using poor local subgrade materials because people then did not have the geotechnical knowledge of today and did not anticipate the large increase in loading and traffic volumes. The poor subgrade materials include (but are not limited to) low or high-plasticity clays, organic soils, cinders, and peat, in addition to degradable and uncompactible materials such as tree stumps and large boulders.
Ballast pockets often trap water within the pocket (see Figure 1), commonly referred to as the “bathtub effect”, which keeps the subgrade material at the ballast-subgrade interface at a high-moisture level, which typically has a significantly lower strength than the same material in a dry condition (Li, 2018).
An additional mechanism that may lead to rapid track geometry degradation is degraded ballast and fine material contaminating the ballast in the ballast pocket. Previous studies and historical knowledge show that fine-contaminated ballast can reduce track strength, stiffness, and drainage, especially when wet (Wilk et al., 2019), often leading to higher rates of the settlement in the ballast layer.
[adsanity id=”96962″ align=”aligncenter”/]
Therefore, it is believed that successful remediation of ballast pockets requires reducing or eliminating the soft subgrade embankment deformation. Addressing fine-contaminated ballast near the surface may be an additional need depending on the situation. Remediation strategies to reduce the track geometry degradation at ballast pockets include:
- Installing ballast drains at the low ballast pocket region to remove excess water and increase embankment strength,
- Stabilizing the subgrade embankment material (grout columns for example) to directly increase embankment strength, or
- Stabilizing the upper ballast (geosynthetics or hot-mixed asphalt (HMA)) to improve stress distribution and reduce the stress in the lower embankment. A second benefit of stabilizing the ballast layer is the removal of fouled material which may be detrimental to track geometry, especially when wet (Wilk et al., 2019).
Ballast Pocket Case Study
The first case study involves the stabilization of a ballast pocket along a 500-ft clay fill embankment on a Norfolk Southern track with geogrid and ballast drains. The embankment is approximately 100-years old and the track carries about 17 MGT of railway traffic per year.
Prior to remediation, maintenance was required about once a week to maintain proper track geometry. Ground Penetrating Radar (GPR) and Cone Penetration Tests (CPT) were used to characterize the site and determine the locations of the deepest ballast pockets. The results from the site characterization showed ballast pockets extending 7-ft to 8-ft deep and soil subgrade resilient modulus values from cone resistance testing between 2.5 to 4.0 ksi, which relates to a moderately soft subgrade (Read et al., 2011).
In 2012, triaxial geogrid and ballast drains were installed along the embankment. The triaxial geogrid was installed 12-inches below the bottom of the tie to ensure the geogrid would not be damaged during tamping and clean ballast was installed to ensure the rock/geogrid interaction was optimized and remove any fine-contaminated ballast near the surface. A photograph of the geogrid installation is shown in Figure 2. The benefits of the geogrid include stabilizing and strengthening the upper ballast region, prevention of downward ballast migration, and improving load distribution to the lower embankment. Two ballast drains were installed at the lowest ballast regions found from the GPR investigation with the purpose of removing water trapped within the ballast pockets, resulting in improvement of the shear strength of the clay embankment.
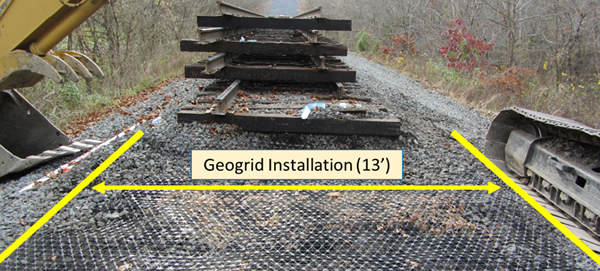
Ballast Pocket Case Study Results
Immediately after remediation, required surfacing dropped from weekly to yearly. In recent years, it has increased to about five times a year (shown in Figure 3), likely due to asymmetrical lower embankment movement which is causing the geogrid to deform and migrate, reducing its effectiveness. More information about the lower embankment movement can be found in another publication (Li, 2018) and that aspect of the study emphasizes the need to investigate the lower embankment and be aware of transition areas when the geogrid ends. Due to the significant reduction in maintenance requirement, a cost-benefit analysis showed the payback period of the installation was less than a year.
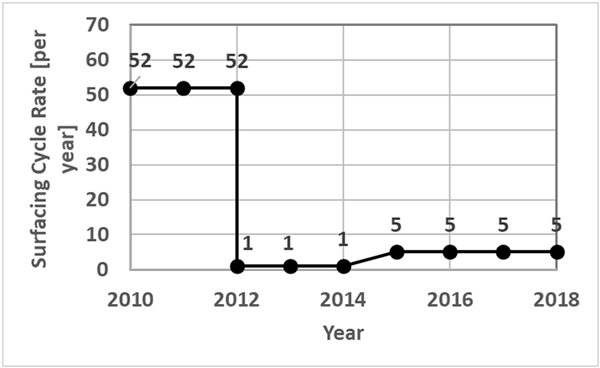
Railroad Applications: Subgrade Pumping in Railroad Cut
Railroad track located in cuts or below-grade regions often experience increased track geometry degradation resulting from drainage and mud pumping issues. Since the track in these situations are located at a low-point, surrounding water tends to drain into the track and leaves a water table presence only a few inches below the track or even above the track. Draining the excess water near the track is difficult without significant remediation efforts. Figure 4 shows an illustration of a flooded cut.
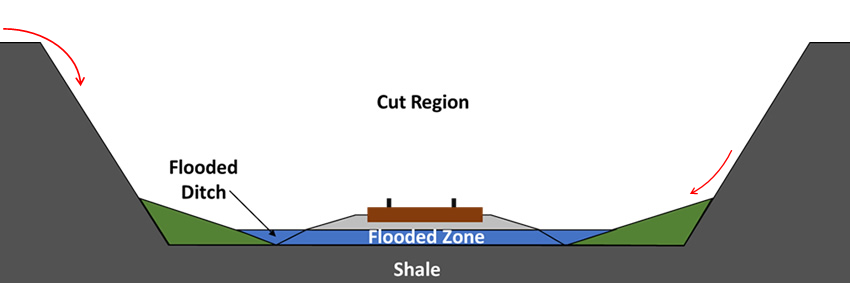
One problem of a flooded track on a shale subgrade is that the water can weaken the shale subgrade and increase the risk of subgrade particles pumping up into the ballast, contaminating the ballast with fines. This can result in increased settlement, especially when wet (Wilk et al., 2019), so reducing fines in ballast is beneficial to track performance.
Fine-contaminated ballast from subgrade infiltration is overall rare in railroad tracks as past investigations showed that 5% of fines comes from subgrade infiltration, as opposed to 73% from ballast breakdown, 7% from surface infiltration, and 15% from other sources (Selig et al., 1992). However, the study also showed that fines from subgrade infiltration can be prevalent if the subgrade consists of materials that can easily be broken down when saturated (shales or mudstones for example). This suggests that remediation for fine-contaminated ballast will differ depending on how the fines contaminate the ballast. For example, an appropriate solution for subgrade pumping will not be appropriate if the fines are from ballast breakdown or infiltrate from the surface.
Flooded Cut Case Study
The second case study involves Norfolk Southern track located within a cut region that is approximately 20 feet lower than the surrounding topography, as shown in Figure 4. The underlying subgrade consists of relatively impermeable silts and shales with very little capacity for drainage. The track is located between two other tracks, further inhibiting the ability to drain the water in the location. The track has an annual tonnage of approximately 20 MGT.
Due to the depressed track orientation, standing water is often observed in ditches along the track and often corresponds with mud pumping, which can increase track degradation rates. Figure 5 shows the cut region, the excess water effects, and mud pumping in the track.
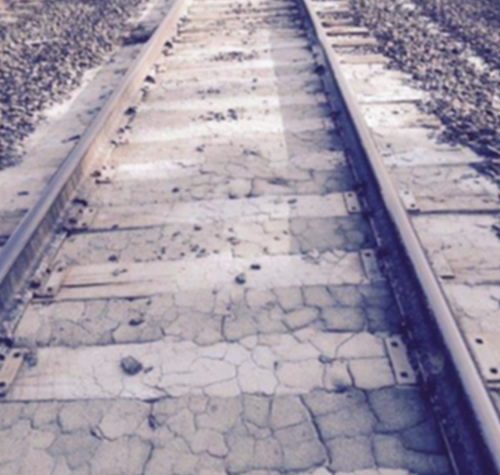
The fines were determined to be from the shale subgrade degrading into fines, then pumping into the surface based on a visual analysis of the fines and trench excavations. In these situations, draining excess water or installing a barrier layer would address the underlying mechanisms producing the fine-contamination because the saturated conditions allows the shale to break up and pump upwards. Due to the difficulty of draining the excess water in this location, barrier methods were explored. Three different geosynthetic test sections and a control section were installed to compare the effectiveness of the geosynthetic systems. The three tested geosynthetics were: Biaxial Geogrid bonded to a geofabric, Tracktex, and 6-inch high Geoweb underlain by geofabric. Each of these geosynthetic systems were tested in an 80-ft section along with a fourth 80-ft control section that had no remedial geosynthetic. Each of the remedial systems is a separation layer consisting of a geofabric or cloth, which provided essential fines migration capabilities. In addition, the biaxial geogrid should provide some resistance to lateral deformation, and the geocell should afford even higher resistance to lateral deformation of the overlying subballast.
The installation occurred in April 2016 and the design details and the test layout are shown in Figure 6.
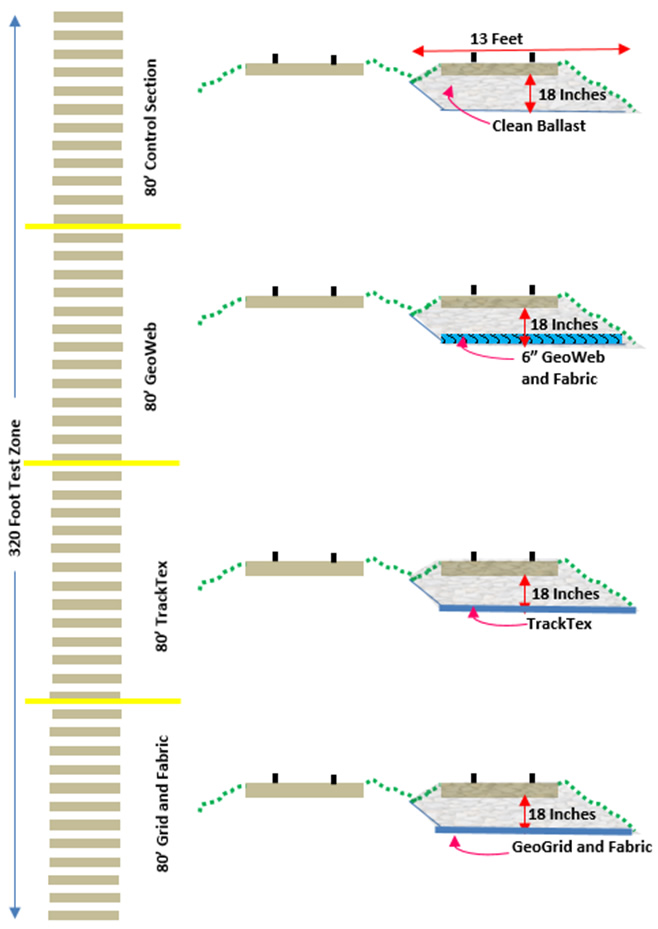
Flooded Cut Case Study Results
To quantify the ability of the geosynthetics to reduce subgrade pumping and fine particles within the ballast, physical samples of shoulder locations were taken in each of the test and control sections. A site visit in July 2018 occurred to assess the ballast and geosynthetic condition after approximately 40 to 50 MGT. The ballast was exposed by backhoe and used to gather samples from different locations and elevations for a gradational assessment. Shoulder cleaning had been done in the control ballast zone in early 2018, so samples were collected immediately adjacent to the control zone in (representative) undisturbed ballast.
The percentage of fine material passing the #4 sieve and the associated ballast fouling index (FI) for each of the geosynthetics showed significant improvement compared to the control samples. The FI provides a practical recognition of the deleterious effects of fines in the ballast, and thus gives the fines percentage extra statistical weight. It is defined as the summation of percentage by weight of ballast material passing the 4.75 mm (No. 4) and the 0.075 mm (No. 200) sieves (Li et al., 2016). For both metrics, the three test locations showed about a 70% reduction in fines within the ballast than the control. This is shown in Figure 7.
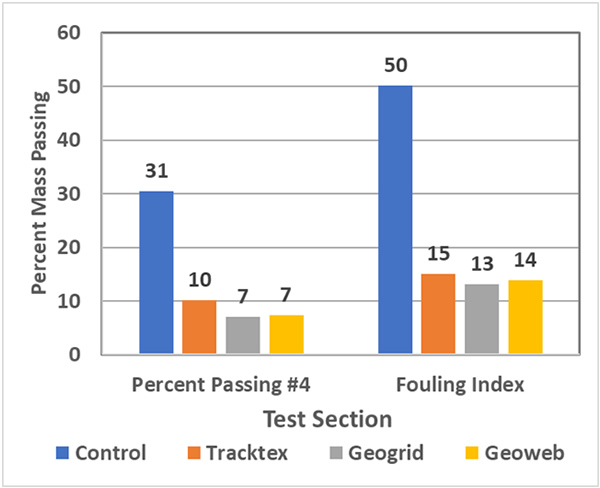
In addition to the beneficial fine filtering effects afforded by the geofabrics, the presence of reinforcement grids or cells that some of the systems have is designed to provide interlocking support of the ballast, even when fines begin to accumulate near the base. The geogrids and cells also provide tensional resistance to dynamic deformation as they engage, thus developing a stiff matt-like foundation and reducing ballast wear.
Railroad Applications & Geosynthetics: Takeaways
Ballast pockets and flooded cuts represent two subgrade issues that result in increased levels of track maintenance and reduced operational capacity. Ballast pockets develop from the progressive deformation of the subgrade and continual addition of ballast to maintain track geometry. Ballast drains are the common fix, which can have mixed results when used by themselves, but the combination of ballast drains to remove excess water, renewal of the top-12 inches of ballast to remove fine particles, and the additional installation of geogrid 12-inches below the surface to further strength the ballast layer and improve load distribution reduced required maintenance from weekly to yearly for this particular case study. To optimize the process, investigation methods such as GPR or Cone Penetration Tests can be used to identify the deepest ballast pocket location.
Flooded cuts present an issue because excess water from the surrounding region tends to accumulate in the tracks, which is the low region in the area. The problem can be accentuated if the subgrade is easily broken (shale, for example) and fine particles can upwardly pump into the ballast, contaminating the ballast section. Typical drainage techniques are often not feasible due to limitations on where to redirect the water and surrounding tracks. In the case study, geosynthetics were used as a barrier layer between the ballast and shale subgrade to prevent upward fine pumping. The geosynthetics successfully reduced the fine levels in the ballast, which can reduce the needs for ballast maintenance.
These two case studies show that common subgrade issues can be remediated with geosynthetics if the root cause or causes are properly addressed. TTCI plans to continue investigating these and other situations to better determine root causes and how geosynthetics and other remedial solutions can address these issues.
ACKNOWLEDGEMENTS
The authors would like to acknowledge support from Norfolk Southern and the Association of American Railroads (AAR) Strategic Research Initiative (SRI) Program for project funding. References for this article follow the About the Authors details.
ABOUT THE AUTHORS
Stephen Wilk and Dingqing Li work for the Transportation Technology Center, Inc., part of the American Association of Railroads. Visit TTCI’s site for more railroad applications research information. Colin Basye is a former TTCI/AAR employee (retired). Brad Kerchoff works for Norfolk Southern Corporation.
REFERENCES
American Railway Engineering and Maintenance-of-Way Association. 2018. AREMA Manual for Railway Engineering, Chapter 1 Roadway and Ballast, Landover Maryland, 2012.
Basye, C and Wilk, S.T. (2019). Remediation of Ballast Pockets in a Railway Environments. 2019 American Railway Engineering and Maintenance-of-Way Association Conference. Minneapolis, MN.
Li, D., Hyslip, J., Sussmann T., and Chrismer, S. (2016). Railway Geotechnics. CRC Press. Boca Raton, Fl.
Li, D. (2018). 25 years of heavy axle load railway subgrade research at the Facility for Accelerated Service Testing (FAST). Transportation Geotechnics. Vol 17, Part A, Pg 51-60.
Read, D. Thompson, R., Hyslip, J., and Hailey, R.S. (2011). Investigation of Track Geometry Problems on Norfolk Southern Captina Secondary. Technology Digest. TD11-049, TTCI, Pueblo, CO.
Selig, E.T., DelloRusso, V., and Laine, K.J. (1992). Sources and Causes of Ballast Fouling. Report No R-805. Association of American Railroads. Technical Center, Chicago, 1992.
Wilk, ST., Basye, C., Brice, M., Baillargeon, J. (2019). Influence of rain events on performance of fine-contaminated ballast. International Heavy Haul Conference – 2019. Narvik, Norway.