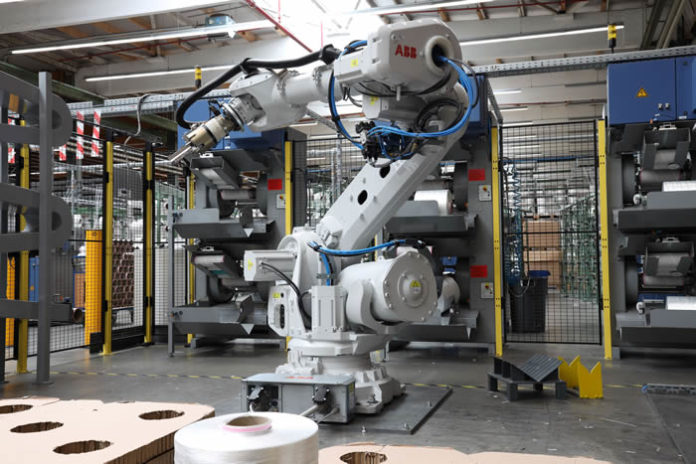
The geosynthetics field developed out of—and remains deeply connected to—textile and fabric manufacturing. Many geosynthetic materials are produced using yarns and numerous manufacturers have other markets into which they sell materials such as fibers and base yarn that they produce.
In a busy manufacturing plant, this involves repeated handling of reels.
Operators use forklifts to move large pallets, and prongs and strap systems can be used to move large rolls of material. Spools of yarn, however, generally require manual handling. These items can weigh nearly 40 lbs each.
HUESKER is now improving safety and reducing strain on factory employees with the use of a robotics prototype in one of its base yarn production systems.
MORE GEO: Register Now for Geosynthetics CQA Week Online Courses
ROBOTICS ON THE PRODUCTION FLOOR
“We have been giving a lot of thought to how to apply robotics and automation in the best possible way for us and our personnel,” says Dr. F.- Hans Grandin, Chairman of the Management Board of HUESKER Group. “When it comes to handling and palletizing twine reels, which can weigh up to 17 kilograms each, the advantages are clear: robots relieve our employees of this strenuous job and give them the opportunity to take on other important tasks.”
The company worked with international robotics pioneer ABB to develop a process-specific robot that picks up finished yarn reels from three production machines in a facility that produces base yarn made from 100% recycled materials. The machines have multiple removal troughs, but their positioning and the weight of the reels are not ergonomic. The spools also differ in diameter and weight. For humans, this is an arduous, repetitive task with a constant risk of injury. For robots, it’s simple reptition.
The prototype robot can even handle payloads up to 150 kg (330 lbs).
The use of robotics takes roughly 2.5 tons per day off the shoulders of the employees, HUESKER notes, and even takes care of stacking the reels in the palletization process.
There remain many tasks that employees must handle manually, such as removing ready pallets and refilling empty cores; but the removal of repetitive lifting risks improves the safety of the facility and ultimately allows the production system to run nearly autonomously.
“We have turned this automation system into a prototype,” says Heinz-Georg Richels, a Technical Manager for HUESKER. “We are using the lessons learned to build further knowledge for robotics in this special field of application. This is because handling thread in synthetic materials is a very complex requirement, for which there are no off-the-shelf systems available.”
The diverse manufacturer sees great potential for robots in its production systems, such as for upstream processes in twine production. These innovations create continuous automation lines, support safer working conditions, and expand the types of employees the company needs for the future of manufacturing (e.g., robotics technicians on the production floor).
Learn more about HUESKER’s innovative manufacturing, geosynthetics, and engineering expertise at www.huesker.com.