A major intermodal logistics facilities and solutions provider for global commodities transport sought to construct new warehouses at a site in Perú. However, poor foundation conditions–clay silt materials, high water table–complicated the plan for new storage yards and a mineral conveyor belt. In lieu of a costly replacement of large volumes of material and increasing the foundation dimensions, the operator improved the soil’s bearing capacity with a geosynthetic solution.
Geocells have increasingly been utilized around the world for load support and reinforcement designs. This is a succinct project story of how and why this is the trend. The work presented here from Prof. Jorge Alva, Jesus Cardozo, M.S., and Daneck Cibej, MBA, is part of Geosynthetica’s GeoAmericas series.
1. INTRODUCTION TO STORAGE YARD PROJECT
By 2011, Impala Terminales Perú began implementing the Expansion and Modernization work for the Callao warehouses in order to improve the work capacity and meet international quality standards. Part of this expansion occurred in the Cormin II and Toromocho warehouses, which presented materials of very low bearing capacity and the presence of high water tables in the initial soil studies due to the proximity to the Pacific Ocean. The presence of these low-quality materials was of concern to the development of the project because it did not ensure proper installation of project structures, such as material conveyor belts or transfer rails; finding a solution to this scenario was a critical point challenging project investment.
Initial proposals opted to use large amounts of replacement material and/or moderately increase the dimensions of the foundation, the use of deep foundations using concrete piles was also sought. All these alternatives were proposed in order to improve the soil’s load-bearing capacity and minimize settlements that could lead to serviceability failure unsettle the large project structures.
MORE GEOAMERICAS: QC and Leak Location of a Bituminous Liner in the Arctic
The main problem was with the Cormin II warehouse and the materials conveyor belt, as they had poorer quality materials (clayey silts); these areas were large, so the volume of work was very high. Choosing one of the alternatives indicated above involved a large investment for the owner, so it was ideal to find new proposals that would be profitable and that would meet the needs of the project.
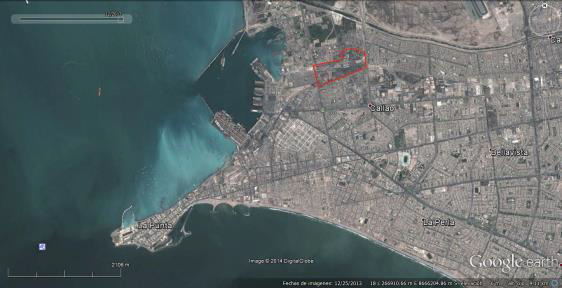
Among these new alternatives, geosynthetic materials is one of them, which, applied to traditional engineering, provide very positive results. One of these materials is load-bearing geocells, implemented to improve land of low bearing capacity by improving the mechanical behavior of soil that they contain and redistributing loads more efficiently. As a result of these effects, the reduction of settlements and the increase of the ground’s allowable bearing capacity is observed.
Figure 2 shows (a) the failure mechanisms for ordinary ground without reinforcement and (b) the failure mechanisms for ground reinforced with the geocell system. Figure 3 shows the geocell reinforcement mechanism.
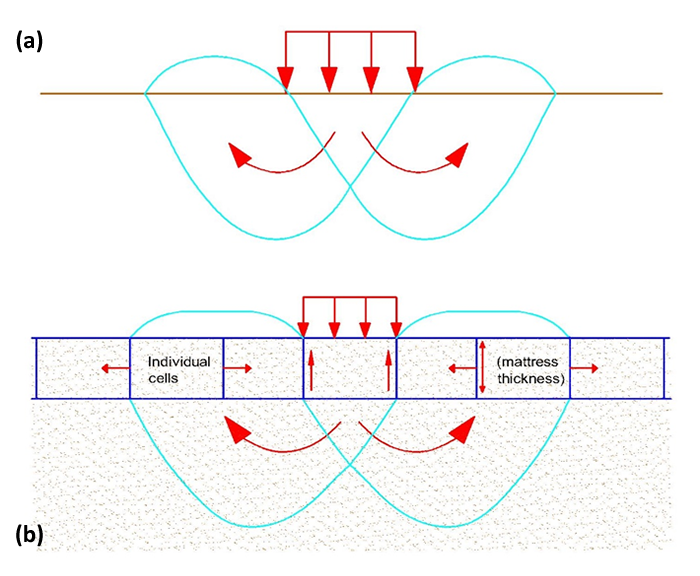
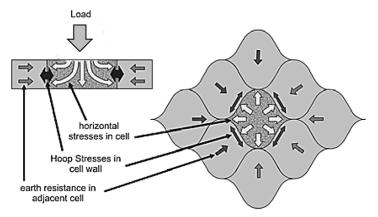
Due to the fact that the solutions proposed preliminarily were unprofitable and required a long time for installation, Impala Terminals Perú decided to carry out the land improvement with the geocell system for load bearing.
In his book Designing with Geosynthetics, Koerner (2005) suggests that the contribution of the geocells system in a foundation is given by Eq. 1, included in the load capacity equation posed by Terzaghi according to Eq 2.
Equation 1
Equation 2
Where:
σh = Average horizontal stress in the geocell
δ = Interaction angle between the walls of the geocell and fill material
2. OBJECTIVES
The following paper has the following objectives:
- To present the solution to the problem presented by the Callao warehouse foundations.
- To present the benefits of the geocells system applied to foundations.
3. BEARING CAPACITY SOLUTION
Due to what is explained above, a solution was sought that would be able to avoid major earthworks, and oversized footings, would not represent a large economic cost, and would have a smaller impact on the environment.
The proposal was divided into two areas, first, the foundation for the slabs of the storage yards, and second, the foundations of the walls of the warehouses; the latter was also used for the foundation of the freight train that supplied the conveyor belt (Andex del Norte – 2011).
The first proposal was intended to improve load distribution from 340 kPa below the slab to a stress of 100 kPa of the natural ground at the lowest possible depth, which was achieved with one layer (1) of geocell 150 mm thick and additional filling base material of 350 mm; in addition to these materials, a 50 mm layer of tamped material was placed on top of the geocell (see Figure 4).
The second proposal was intended to improve the allowable capacity of the land from 0.50 kg/cm2 of the natural ground to a capacity of 1.50 kg/cm2 carried by the foundations of the walls of the warehouses; the effects of settlement were also minimized by the aforementioned issues; all of these facts were achieved with a reinforcement package consisting of two (2) layers of 150 mm geocells, and additional filling with base material of 350 mm; in addition to these materials, one additional 50 mm layer of tamped material was placed, divided into 25 mm above each geocell (See Figure 5).
MORE GEOAMERICAS: Oil Terminal Modernizes with Concrete-Filled Geotextile Tubes
All proposed solutions with the geocell system took into account the high water table present in the project; methods for controlling groundwater flow were also used via subdrains over material (American Association of State Highway and Transportation Officials-AASHTO).
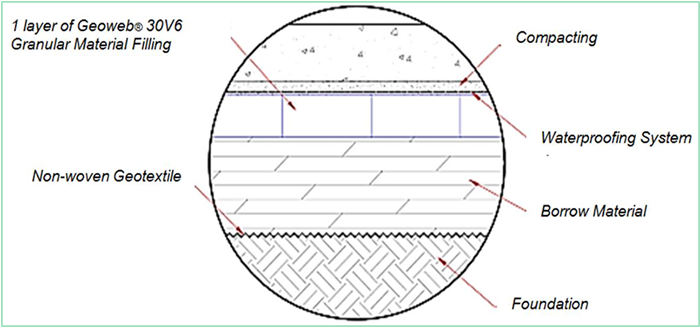
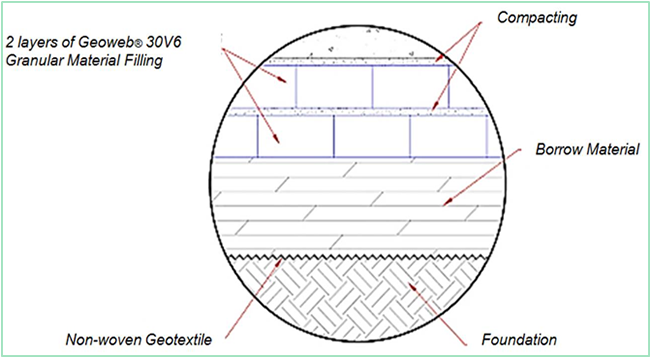
3.1 Installation of the geocell system
The installation process was conducted according to the specifications in the technical dossier; proper drainage of the foundation was controlled using Over material; we proceeded to leveling and then placing the non-woven separation geotextile; finally the reinforcement packets, including the geocells, were placed.
As quality measures, there was adequate compaction monitoring at 95% of the modified compacting elements, placement monitoring, and visual monitoring of the geocell materials.
Figures 6 and 7 show the initial state of the subsoil of the project foundations and the placement of the subdrain.
Figures 8 and 9 shows the leveling and the placement of the geocells.
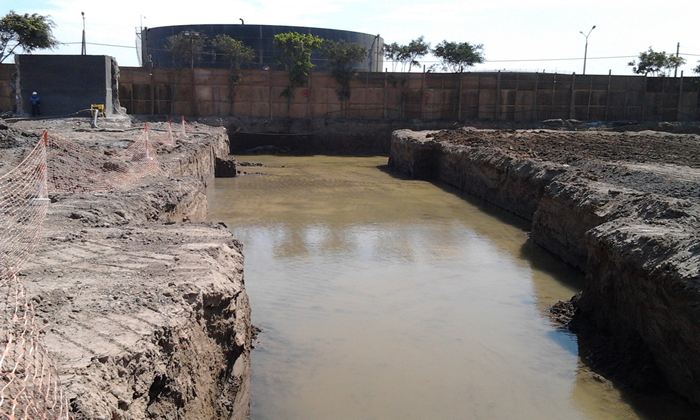
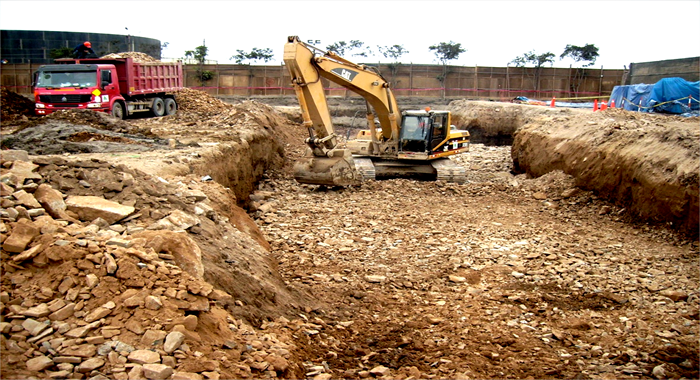
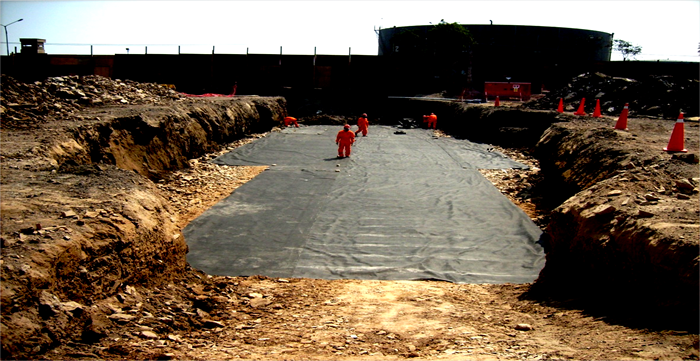
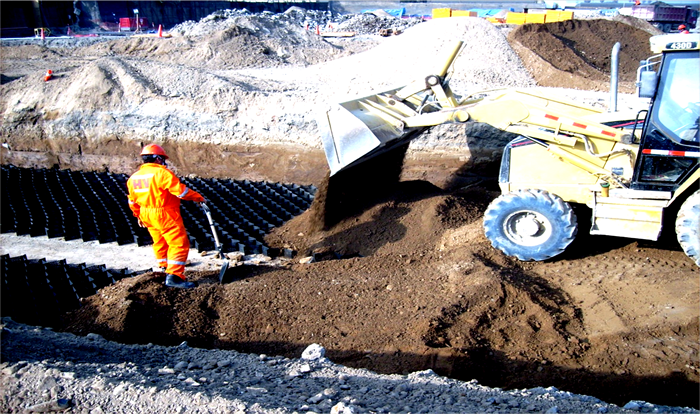
4. MONITORING
To date, the storage container yard slab and the conveyor belt don’t show any problems, which is a clear sign of the contribution of the system to the final solution, thus complying with the initial design requirements that this significant project demanded.
5. CONCLUSIONS
From the submitted report, it can be concluded that:
- The use of adequately arranged and filled cellular containment structures allows distribution of pressures from the ground and external loads more effectively than natural ground, due to the containment and reduced deformation capacity that this gives to the contained material, giving the system better performance than conventional load support.
- Traditional solutions for the project studied were dismissed as unprofitable in comparison with the geocell system.
- The geocell system is an economically viable solution for this medium because the use of replacement material is minimal, its construction is simple, it requires no skilled labor and the performance in its construction is high.
Furthermore, this system represents an environmentally friendly solution. The geocells system has demonstrated adequate performance to this day after all project structures have been implemented.
ABOUT THE AUTHORS
Prof. Jorge Alva is with the National Engineering University, Lima, Perú. Jesus Cardozo, M.S., is President of Andex del Norte S.A – Perú. Daneck Cibej, MBA, is an independent civil engineer in Perú.
REFERENCES
AASHTO. 1993. Guide for the Design of Pavement Structures. Washington, D.C.
Andex del Norte. 2011. Calculation Reports_Foundation Reports – Callao Warehouses Expansion and Modernization Project. Lima.
Koerner, Robert M. 2005. Designing with Geosynthetics. USA.
Portland Cement Association. 1987. Structural Design of Roller Compacted Concrete for Industrial Pavements.
Tanyu et. al. 2013. “Laboratory Evaluation of Geocell Reinforced Gravel Subbase Over Poor Subgrades,” Geosynthetics International, v. 20, no. 2.